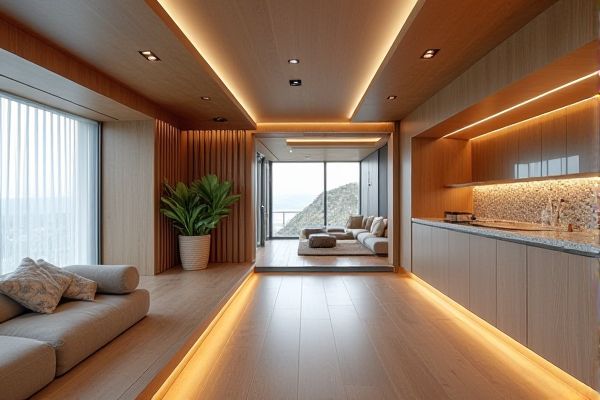
Continuous rail offers seamless, smooth train travel with fewer joints, reducing maintenance needs and enhancing ride comfort, while segmented rail consists of shorter rail sections joined together, making installation and repairs more manageable but potentially causing more noise and wear at the joints. Explore the rest of the article to understand which rail type best suits Your transportation infrastructure needs.
Table of Comparison
Feature | Continuous Rail | Segmented Rail |
---|---|---|
Construction | Single, continuous steel rail | Multiple rail segments joined together |
Expansion Handling | Designed to allow thermal expansion | Expansion managed via gaps or joints |
Maintenance | Lower maintenance due to fewer joints | Higher maintenance because of multiple joints |
Ride Quality | Smoother ride with minimal noise | Potential joints cause vibration and noise |
Durability | More durable with less wear and tear | Edges wear faster due to joints |
Installation Cost | Higher initial cost due to continuous rail | Lower initial cost, easier to install |
Typical Use | High-speed rail, heavy rail lines | Light rail, temporary or flexible tracks |
Introduction to Continuous Rail and Segmented Rail
Continuous rail features long, unbroken lengths of rail that provide smoother rides and reduced maintenance compared to segmented rail, which consists of shorter, bolted sections allowing easier repairs and flexibility for expansion. Segmented rail, while simpler to install and replace, may cause more joint noise and wear, impacting ride quality and longevity. Understanding the differences between continuous and segmented rail can help you choose the best solution for specific railway infrastructure needs.
Definition and Key Features of Continuous Rail
Continuous rail, also known as continuous welded rail (CWR), consists of long sections of rail welded together to form a seamless track without joints. This design reduces vibrations and maintenance needs, providing a smoother and faster ride. Key features include enhanced track stability, decreased wear and tear, and improved durability compared to segmented rails made of shorter, jointed sections.
Definition and Key Features of Segmented Rail
Segmented rail consists of short rail sections joined together by fishplates or bolts, allowing for thermal expansion and ease of maintenance compared to continuous rail. It features gaps between segments that accommodate natural metal expansion and contraction due to temperature changes, reducing the risk of rail buckling. Your choice of segmented rail may improve track flexibility and lower initial installation costs but requires more frequent joint inspections.
Material Composition and Manufacturing Differences
Continuous rail is typically made from high-quality steel alloys with uniform composition, produced through a hot rolling process to ensure structural integrity and smooth surface finish. Segmented rail sections are often composed of similar steel grades but may exhibit slight variations due to casting or welding techniques used to join individual segments. Manufacturing continuous rail involves precision rolling and heat treatment to reduce internal stresses, whereas segmented rail production relies on modular assembly and joint welding, affecting overall material homogeneity and mechanical properties.
Installation Process: Continuous Rail vs Segmented Rail
The installation process for continuous rail involves securing a single, unbroken rail section along the entire track length, minimizing joints and reducing alignment errors. Segmented rail installation requires assembling multiple rail sections with connectors, which can increase installation time and the potential for alignment discrepancies. Continuous rail offers smoother rides and lower maintenance costs due to fewer joints, while segmented rail provides easier handling and flexibility during installation.
Maintenance Requirements and Durability
Continuous rail systems exhibit lower maintenance requirements due to fewer joints, reducing wear and risk of track misalignment compared to segmented rails. Segmented rails, consisting of individual sections joined together, face higher stress concentrations at joints, leading to increased potential for rail fatigue and track deformation. The durability of continuous rails surpasses segmented designs, providing enhanced stability and longer service life under heavy rail traffic conditions.
Performance: Ride Quality and Noise Reduction
Continuous rails provide superior ride quality by minimizing joint impact and vibrations, resulting in smoother train operations compared to segmented rails that have gaps causing noticeable jolts. Noise reduction is significantly enhanced in continuous rails due to fewer expansion joints, which reduces the sound generated by wheel-rail interaction. Segmented rails often produce higher noise levels and less consistent ride comfort because the gaps amplify track irregularities and joint noise.
Cost Comparison and Economic Considerations
Continuous rail offers lower maintenance costs and enhanced durability due to fewer joints, reducing long-term expenses despite higher initial investment compared to segmented rail. Segmented rail has lower upfront installation costs but incurs higher maintenance and replacement expenses because of joint wear and increased risk of mechanical failure. Economic considerations favor continuous rail for high-traffic routes where lifecycle cost efficiency outweighs initial savings.
Best Applications for Each Rail Type
Continuous rails are ideal for high-speed railways and heavy freight lines due to their smooth, uninterrupted surface, which reduces maintenance costs and minimizes vibrations. Segmented rails suit urban transit systems and sections with frequent curves or temperature variations, allowing for easier track adjustments and preventing rail buckling. Choosing the right rail type depends on factors like train speed, track length, climate conditions, and maintenance capabilities.
Future Trends in Rail Track Technology
Continuous rail offers smoother rides and reduced maintenance by eliminating joints, while segmented rail provides easier installation and flexibility in curved or complex track layouts. Future trends emphasize smart monitoring systems and advanced materials to enhance durability and safety in both rail types. Your rail infrastructure investments benefit from integrating these innovations to optimize performance and lifecycle costs.