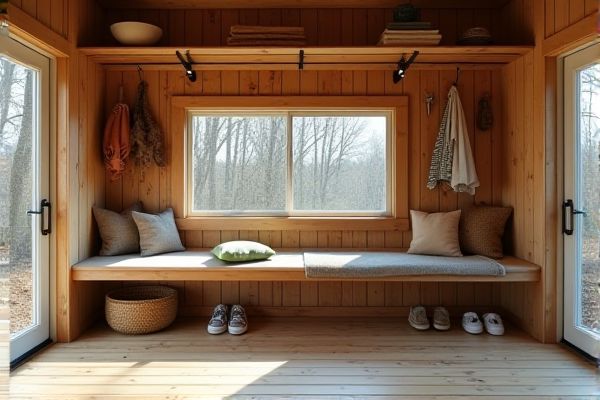
Overhead storage maximizes vertical space by utilizing wall-mounted shelves or cabinets, ideal for keeping frequently used items visible and accessible, while under bench storage offers concealed compartments that help maintain a clean, uncluttered workspace. Discover how choosing the right storage solution can enhance your organization and functionality by reading the rest of the article.
Table of Comparison
Feature | Overhead Storage | Under Bench Storage |
---|---|---|
Location | Mounted above head level, on walls or ceilings | Integrated below countertops or workbenches |
Accessibility | Requires reaching or step stools | Easy access while standing or sitting |
Space Utilization | Maximizes vertical space, frees up floor area | Makes use of unused bench base area |
Storage Capacity | Suitable for lightweight and rarely used items | Can store heavier and frequently used tools or equipment |
Safety | Risk of falling items if not secured properly | Generally safer as items are enclosed and stable |
Installation | Requires strong wall or ceiling anchors | Built-in during bench construction or retrofitted |
Ideal Use Cases | Garage, workshop, kitchen for infrequently accessed goods | Workshops, kitchens, labs for daily-use tools and supplies |
Introduction to Overhead Storage vs Under Bench Storage
Overhead storage maximizes vertical space by utilizing wall-mounted shelves and cabinets, ideal for keeping frequently used items within easy reach. Under bench storage offers accessible, organized compartments beneath work surfaces, perfect for tools and materials needing quick access without cluttering your workspace. Choosing between the two depends on your workspace layout, storage needs, and the balance between accessibility and spatial efficiency.
Space Optimization: Overhead vs Under Bench
Overhead storage maximizes vertical space, freeing up floor and bench areas for more efficient workflow, ideal for smaller rooms or workshops with limited floor space. Under bench storage utilizes the area beneath work surfaces, keeping tools and materials within easy reach while maintaining a clean and organized bench top. Your choice depends on balancing accessibility with spatial constraints to optimize the overall workspace layout.
Accessibility and Convenience
Overhead storage offers easy visibility and quick access for frequently used items, making it ideal for tools and materials needed on a daily basis. Under bench storage provides convenient reachability while seated or working at the bench, reducing the need to stretch or bend excessively. Both storage types enhance workflow efficiency by catering to different ergonomic and organizational needs in workspace design.
Safety Considerations for Each Storage Type
Overhead storage poses safety risks such as falling objects and requires secure mounting hardware to prevent accidents, especially in high-traffic areas. Under bench storage reduces the risk of falling hazards but must ensure clear access to avoid tripping and maintain ergonomic reach for users. Proper labeling, load limits, and routine inspections are essential safety measures for both storage types to minimize injury risks.
Aesthetic Impact on Room Design
Overhead storage maximizes vertical space, creating a clean and open floor area that enhances room spaciousness and modern aesthetics. Under bench storage seamlessly integrates into furniture design, maintaining visual continuity and reducing clutter at eye level for a streamlined look. Choosing between the two depends on the desired balance between accessibility, room height, and the overall design theme.
Cost Comparison: Overhead vs Under Bench
Overhead storage typically incurs higher installation costs due to the need for reinforced supports and specialized mounting hardware, whereas under bench storage is generally more cost-effective with simpler construction and integration into existing furniture designs. Maintenance expenses for overhead units can also be greater, requiring periodic inspections to ensure safety and stability. Under bench storage offers a budget-friendly solution with easier access and lower long-term upkeep costs, making it ideal for both residential and commercial spaces.
Installation and Maintenance Differences
Overhead storage typically requires more complex installation involving wall anchors or ceiling mounts, ensuring secure support for heavy items, whereas under bench storage often involves simpler assembly or sliding mechanisms fixed directly to cabinetry. Maintenance for overhead storage includes regular checks for stability and dust accumulation on higher surfaces, while under bench storage demands frequent cleaning to prevent dirt buildup and ease of access. Your choice depends on balancing installation effort with ease of upkeep based on space and usage preferences.
Ideal Use Cases for Overhead Storage
Overhead storage is ideal for keeping frequently used tools and materials within easy reach while freeing up valuable floor and bench space, making it perfect for workshops and kitchens with limited room. This storage solution enhances organization by allowing users to categorize and access items efficiently at eye level or slightly above. Overhead units are particularly beneficial in environments requiring quick tool retrieval and optimized workspace ergonomics.
Ideal Use Cases for Under Bench Storage
Under bench storage is ideal for workshop environments where quick access to tools and materials is essential, keeping work surfaces clear while maintaining organization. It excels in spaces with limited vertical clearance or where overhead storage may obstruct lighting or ventilation. This type of storage is also suitable for heavier items that require sturdy, stable support close to the work area.
Making the Right Storage Choice for Your Space
Choosing between overhead storage and under bench storage depends on maximizing available space and accessibility. Overhead storage is ideal for keeping frequently used items within easy reach while freeing up floor area, whereas under bench storage offers concealed, convenient compartments perfect for tools or materials in tight workshops. Your decision should consider workflow efficiency, safety, and the specific dimensions of your room to optimize organization and usability.