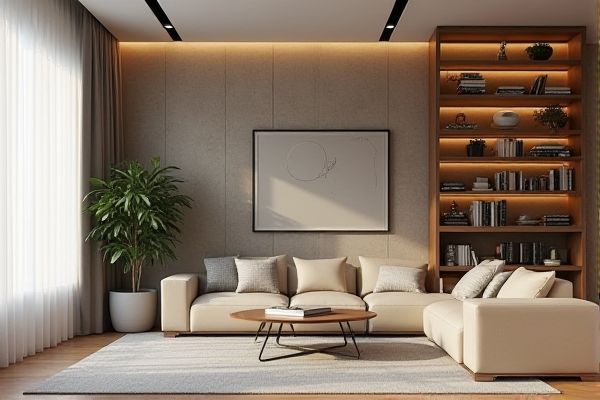
Tower systems maximize storage density by utilizing vertical space with tall, narrow units ideal for small footprints, while vertical shelving offers flexible, easily accessible storage with adjustable shelves suitable for varying item sizes. Discover how each solution can optimize Your storage needs by exploring the advantages and best applications in the full article.
Table of Comparison
Feature | Tower System | Vertical Shelving |
---|---|---|
Design | Compact, multi-level storage units | Single or multiple upright shelves |
Space Efficiency | Maximizes vertical space in a small footprint | Requires more floor space for wider units |
Accessibility | Easy access to multiple levels, often rotating or sliding | Direct access from front, no moving parts |
Use Cases | Ideal for offices, libraries, and archives | Common in retail, warehouses, and garages |
Installation | May require assembly and fixed installation | Simple assembly, often modular |
Load Capacity | Typically supports moderate weight per shelf | Can support heavy loads depending on design |
Cost | Generally higher due to complexity and materials | Usually more affordable and flexible |
Introduction to Tower Systems and Vertical Shelving
Tower systems maximize vertical storage space by stacking items securely, ideal for warehouses seeking efficient use of height. Vertical shelving offers easy access to goods with adjustable shelves suitable for varied item sizes, enhancing organization and inventory management. Your choice depends on storage volume and accessibility requirements, ensuring optimal warehouse layout and operational efficiency.
Core Differences Between Tower Systems and Vertical Shelving
Tower systems utilize a cube-like storage design that maximizes space by stacking items vertically in separate bins, ideal for small parts and tool organization. Vertical shelving consists of tall, upright shelves that accommodate larger items with easy visibility and accessibility, optimized for bulk storage and inventory management. The core difference lies in tower systems focusing on compact, modular bin storage, whereas vertical shelving emphasizes open, tiered sections for varied item sizes.
Space Utilization: Tower Systems vs Vertical Shelving
Tower systems maximize space utilization by offering compact, multi-level storage that efficiently stacks items vertically within a confined footprint. Vertical shelving provides flexible, open access to a variety of items but often requires more floor space due to its wider and less dense arrangement. Your choice depends on whether you prioritize high-density storage with minimal space (tower systems) or ease of access and visibility (vertical shelving).
Storage Capacity and Flexibility Comparison
Tower systems offer enhanced storage capacity by utilizing a modular design that maximizes vertical space and allows easy expansion, making them ideal for growing inventory needs. Vertical shelving provides flexibility through adjustable shelves and easy access, accommodating a wide variety of item sizes and shapes within a more compact footprint. Comparing storage solutions, tower systems excel in high-density storage efficiency, while vertical shelving offers superior adaptability for dynamic storage requirements.
Accessibility and Workflow Efficiency
Vertical shelving maximizes space by organizing items vertically, but tower systems enhance accessibility by providing rotating or pull-out compartments that reduce retrieval time. Your workflow efficiency improves with tower systems due to easier visibility and quicker access to frequently used materials, minimizing movement and search effort. Vertical shelving offers high density storage but can slow down task completion when items are less reachable or require extensive bending or stretching.
Installation and Maintenance Requirements
Tower systems typically require more complex installation involving precise alignment and anchoring to ensure stability, while vertical shelving can often be assembled quickly with modular components. Maintenance for tower systems involves regular inspections of mechanical parts and safety features to prevent malfunction, whereas vertical shelving demands less frequent upkeep, focusing mainly on load checks and structural integrity. Your choice depends on how much time and resources you are willing to allocate for installation and ongoing maintenance.
Safety and Ergonomics Considerations
Tower systems provide enhanced safety by offering enclosed storage that minimizes the risk of items falling, while vertical shelving requires careful organization to prevent accidents. Ergonomically, tower systems often feature adjustable shelves and easy access panels that reduce strain on Your back and improve reach, whereas vertical shelving may demand frequent bending or stretching. Choosing tower systems ensures better protection and comfort for workers in environments demanding secure and efficient storage solutions.
Cost Analysis: Investment and Operational Expenses
Tower systems generally require a higher upfront investment compared to vertical shelving due to their advanced automation and technology integration, which can lead to increased capital expenses. Operational costs for tower systems tend to be lower over time as they improve storage density and reduce labor expenses, whereas vertical shelving incurs ongoing manual handling costs and may require more frequent maintenance. Your choice should weigh the initial capital expenditure against potential long-term savings in operational efficiencies.
Industry Applications and Best Use Cases
Tower systems excel in warehouses and distribution centers that require high-density storage with automated retrieval for small to medium-sized items, enhancing order picking speed in e-commerce and pharmaceutical industries. Vertical shelving is best suited for retail, libraries, and archival storage where easy access and manual handling of larger or irregularly shaped items are needed. Both systems optimize space utilization, but tower systems offer superior integration with automation for high-throughput environments, while vertical shelving provides flexibility for varied inventory types and sizes.
Choosing the Right Storage Solution for Your Needs
Tower systems offer compact, multi-level storage ideal for maximizing vertical space in small areas, while vertical shelving provides easy access and flexibility for frequently used items. Your choice depends on the type and volume of items you need to store, with tower systems suited for organized, high-density storage and vertical shelving better for quick retrieval. Assess your space constraints and workflow requirements to determine which solution optimizes efficiency and accessibility.